Fig. 4.1
Instrument for use in da Vinci® S and Si. (a) I instrument housing, S shaft. (b) W wrist, E end effector. (c) Discs on back of instrument housing that transmit motions to wrist and end effectors via cables that run through the shaft

Fig. 4.2
Instrument for use in da Vinci® Xi. (a) I instrument housing, S shaft. (b) W wrist, E end effector. (c) Discs on bottom of instrument housing that transmit motions to wrist and end effectors via cables that run through the shaft
Types of Instrument Malfunctions
There are two major types of instrument malfunctions: mechanical and electrical. A mechanical malfunction refers to a physical defect in a robotic instrument that compromises normal range of motion and/or function. Although there is a wide range of possible mechanical malfunctions, they all generally inhibit the surgeon’s ability to complete an operation. For example, they may lead to an increase in operating room time as the surgical team attempts to evaluate and manage the malfunction, an increase in the cost of surgery as these malfunctions generally require that the robotic instrument be replaced, and an increase in the risk for surgical complications.
The most commonly reported sites of mechanical malfunctions are the instrument wrist and end effector. In a retrospective review of all reported robotic instrument malfunctions in the United States Food and Drug Administration (US FDA) Manufacturer and User Facility Device Experience (MAUDE) database between January 2009 and December 2010, Friedman et al. found that 285/565 (50.4%) of all reports were mechanical malfunctions at the wrist or end effector [3]. Instrument defects at the wrist generally decrease range of motion, while those at the end effector generally decrease the specific functionality of the instrument; instrument defects at both sites inhibit the surgeon’s ability to operate.
Instruments with articulating jaws, such as needle drivers, grasping retractors, and scissors, are inherently more prone to end effect malfunctions, and they may present in a variety of different ways. In a case report by Park et al., the joint bolt of a ProGrasp™ (Intuitive Surgical, Inc., Sunnyvale, California, USA) forceps became loose which decreased the ability of the instrument to grasp tissue during robotic radical prostatectomy. As the loosened bolt also prevented the ProGrasp™ forceps from being removed through the robotic trocar, the ProGrasp™ was removed with the robotic trocar en bloc. A second bedside assistant assisted with the remainder of the case in place of the ProGrasp™ forceps, and the surgical team was able to complete the procedure with no complications [6]. Also, bending of the end effectors may result in misalignment of the articulating jaws, decreasing their functionality. This may result from instrument mishandling during sterile processing, improper storage, and aggressive intraoperative use. Although reports regarding bending of the end effectors are limited, we frequently encounter this at our institution. Furthermore, there may be instances when a piece of an end effector breaks off into the operative field (Fig. 4.3a, b). Instrument fragmentation requires that the surgeon look for the broken piece and extract it from the patient’s body. In another case report by Park et al., one of the jaws of a needle driver broke off into the surgical field during robotic radical prostatectomy. The surgeons were able to find the broken jaw of the needle driver and extract it from the patient using a laparoscopic grasping forceps [7].


Fig. 4.3
(a) Circle highlights missing end effector on permanent cautery hook. (b) Oval highlights missing end effector of permanent cautery hook found on retroperitoneal fat
Mechanical malfunctions also occur at the shaft. In the aforementioned study by Friedman et al., the authors found that shaft malfunctions accounted for 76/565 (13.5%) of all reported instrument malfunctions [3]. Instrument shaft defects may be caused by instrument collisions with robotic ports/cannulas and arms. While collisions with robotic ports/cannulas generally cause trauma along the vertical axis of the shaft, collisions with robotic arms generally cause trauma along the perpendicular axis of the shaft. These collisions may cause peeling, bending, cracking, or breaking of the instrument shaft [2, 3].
Furthermore, mechanical malfunctions may occur at the cables that run from the instrument housing to the wrist and end effectors. In the aforementioned study by Friedman et al., the authors found that cable malfunctions accounted for 29/565 (5.1%) of all reported instrument malfunctions. Although the cables most commonly malfunction at the instrument wrist and end effector, the cables may malfunction at any point along their length (Fig. 4.4) [3]. Movement of an instrument beyond its normal range of motion or applying excessive force on the robotic instrument may cause the cables to fray, break, or become displaced from their pulleys [8]. Cable malfunctions inhibit the transmission of desired movements to the instrument.


Fig. 4.4
Circle highlights cable fraying on Maryland bipolar forceps wrist at two locations
An electrical malfunction primarily refers to arcing, when an electrical current deviates from its intended course due to an insulation defect. In the aforementioned study by Friedman et al., the authors found that arcing incidents accounted for 156/565 (27.6%) of all reported instrument malfunctions [3]. Although arching may occur with the use of any instrument that utilizes electrocautery, it primarily occurs with the use of monopolar curved scissors. Arcing is particularly problematic as it may cause unintended tissue damage. Stray electrical currents can reach temperatures between 700 and 1000 °C and cause thermal tissue injury [9]. Hollow organs, such as bowel, ureter, and blood vessels, are particularly susceptible to electrical injury as a single spark can cause an immediate or delayed perforation. Arcing may occur due to an insulation defect at the shaft [9] or at the tip cover accessory (TCA) [10, 11]. A TCA is an insulating sleeve that is applied to cover the metallic joint of monopolar curved scissors to allow electrical energy to be transmitted exclusively from the working tips of the shears to the surgical site of interest.
Mendez-Probst et al. studied instrument insulation defects by performing an in vitro study evaluating 37 robotic instruments that had reached the end of their life cycle. After confirming that all instruments did not have any visible insulation defects, the instruments were tested with monopolar current for the presence of stray electrical currents. All 37/37 (100.0%) instruments leaked electrical energy at the end of their life cycle [9]. These results suggest that microscopic insulation defects may cause electrical malfunctions. This is consistent with reports in the traditional laparoscopic literature that have suggested that visually screening instruments to predict insulation failure is limited [12, 13] and is associated with only 10% sensitivity [13].
In a case report by Lorenzo et al., arcing from TCA failure led to perforations of the right obturator and external iliac veins during robotic radical prostatectomy. Bleeding from the right obturator and external iliac veins was controlled by applying bipolar coagulation and placing a 5-mm metallic clip, respectively. Postoperatively, the authors noted two 1 mm holes on the TCA [10]. In a report by Mues et al., arcing from TCA failure occurred in 12/454 (2.6%) robotic surgeries , and 3/12 (25.0%) of arcing incidents caused significant patient injuries. Iatrogenic arcing injuries included damage to the external iliac vein, small bowel, and ureter. All patients required intraoperative repair [11].
Prevention
Preventing mechanical malfunctions involves the identification of defective instruments prior to the start of an operation and taking measures to minimize the chances of an instrument malfunction. In the preoperative setting, the surgical team should carefully inspect all instruments for broken, cracked, or worn components. Damaged instruments should not be used and should be replaced prior to the start of the procedure. Having a dedicated robotic surgical team that is trained in proper instrument handling and knowledgeable about normal instrument function may assist in the preoperative identification of instrument malfunctions [14].
Intraoperatively, it is important to keep the wrists straight when engaging and disengaging an instrument through a robotic port/cannula to prevent damage. When engaging an instrument, the bedside assistant should straighten the instrument wrists by rotating the discs on the instrument housing, rather than manipulating the wrist directly. When disengaging an instrument, the surgeon should straighten the instrument wrists using the master controls. During robotic port placement, it is important to ensure adequate spacing between ports to minimize instrument collisions. Generally, a distance of at least 8–10 cm for the da Vinci® S and Si and at least 6 cm for the da Vinci® Xi should be maintained between each port. The reason for this is because collisions between instruments, which can occur both intra-corporeally and extracorporeally, may cause physical defects.
With regard to the prevention of electrical malfunctions , the importance of proper intraoperative handling of the TCA cannot be overemphasized. Prior to the use of monopolar curved scissors, TCAs should be carefully applied using the prepackaged tip cover applicator in accordance with manufacturer specifications. The insulating TCA should cover the distal end of the instrument shaft and the entirety of the instrument wrist, leaving only the shears non-insulated. Also, similar to the prevention of mechanical malfunctions , measures should be taken to avoid physical damage to TCAs and instrument shafts. Surgeons and bedside assistants should ensure that the instrument wrists are straight prior to engaging and disengaging robotic instruments and appropriately position robotic ports to minimize intra-corporeal instrument collisions [11]. The reason for this is because defects in the TCAs and instrument shafts will compromise their insulating capacities and cause arcing.
Also, TCA failures may occur when the electrocautery settings are above the insulating capacity of the tip covers. Intuitive Surgical recommends keeping the power settings below 3kV. However, electrical malfunctions may still occur while adhering to these recommended power settings. In the previously mentioned report by Mues et al. that detailed 12 TCA failures, all 12/12 (100.0%) failures occurred while using the manufacturer recommended power settings [11]. As such, when using electrocautery, it is important to use the lowest power setting possible for the shortest amount of time necessary to achieve the desired effect.
Risk Factors
Several risk factors are associated with instrument malfunctions. With regard to mechanical malfunctions, instruments with jaws may be at greater risk for malfunction compared to those without jaws. During surgery, these articulating jaws are used to exert considerable forces. However, given the lack of tactile sensation and force feedback during robotic surgery , the surgeon may inadvertently apply excessive force onto the jaws causing them to break [7]. In a report by Kim et al., in which all robotic instrument malfunctions that occurred during surgeries performed by 6 departments at a single institution from July 2005 to December 2008 were retrospectively reviewed, 16/19 (84.2%) instrument malfunctions occurred in instruments with jaws [2].
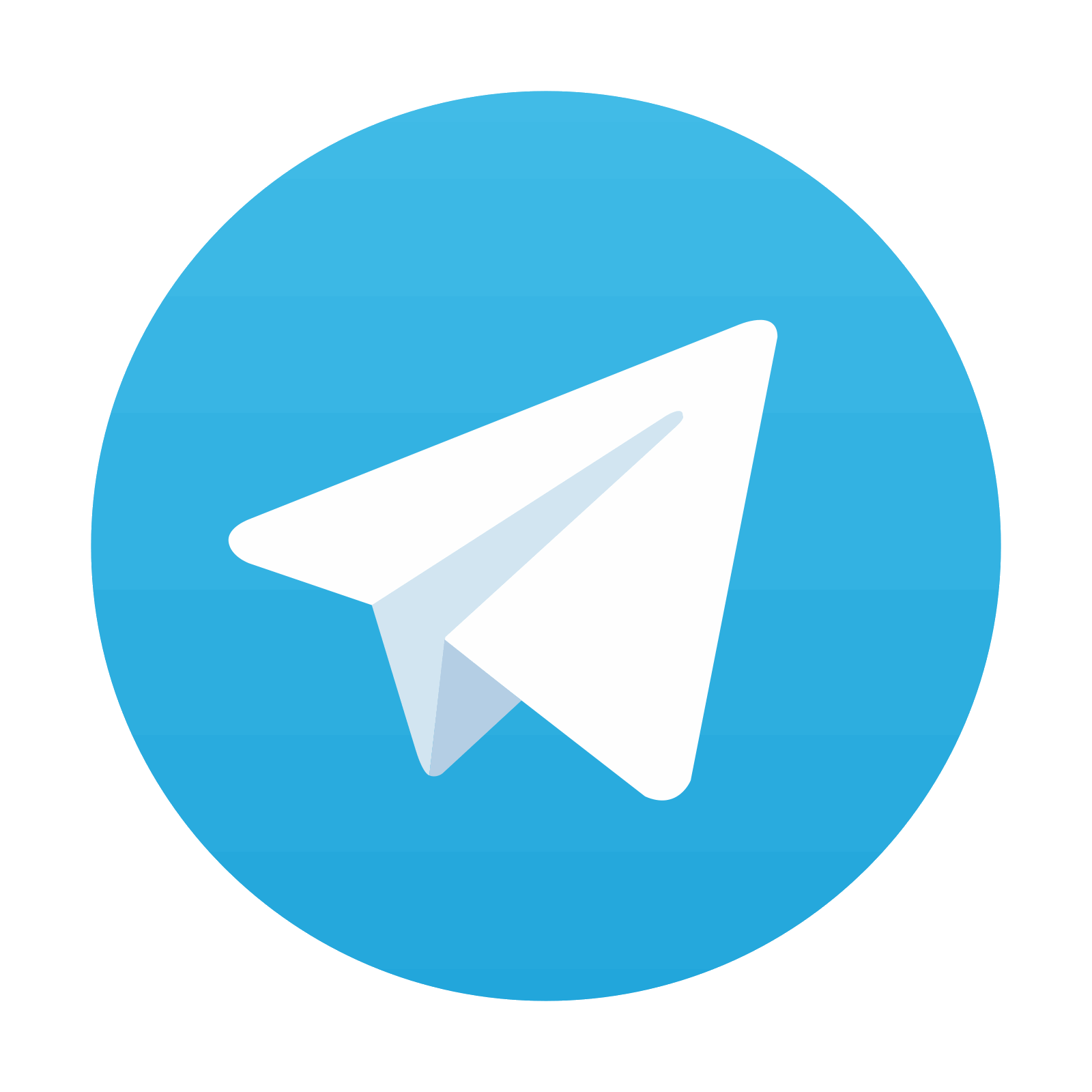
Stay updated, free articles. Join our Telegram channel
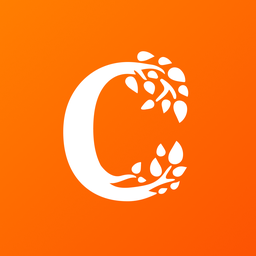
Full access? Get Clinical Tree
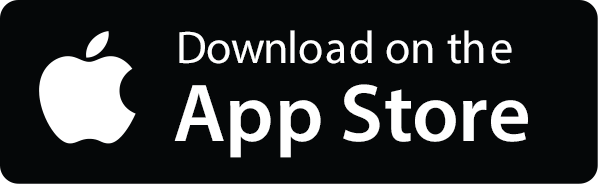
